|
Shop Tour
I use both the forge and the stock removal method of making knives.
I feel both methods produce excelent cutlery when properly heat treated and sharpened.
All of my forged blades I heat treat myself, while most of my stock removal blades
are sent to a professional heat treater, where they receive a sub-zero quench
for added toughness and durability.
|
|
|
My experience in metal working began as a teenager in Europe. I worked as a blacksmith's
apprentice, making knives and cleavers for the local butchers.
I have also worked as an
ornamental ironworker, and in an at foundry as a senior detailer on the fine art and
scultptures made there.
|
Most craftsman are always looking to improve their working techniques.
So I am constantly testing my knives. Pictured to the right,
is D2 blade cutting into the side of a 1964 BMW that was headed for the
junk yard.
Below, is a demonstration of the ABS (American Bladesmith Society)
flex test. After forging of the blade, and a series of cutting tests,
the knife is placed tip down into a vise. It is slowly bent to
at least 90 degrees without breaking.
|
|
|
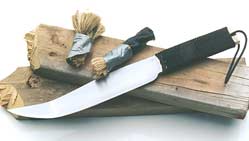 |
After this knife survived the 90 degree bend, the steel sprang back
almost to its original form.
I do not know which of these tests broke my heart more. The bending
of a blade after so much work, or the death of a classic BMW.
|
Home | Ordering Info |
Std. Models |
Available | Show Schedule |
Shop Tour
Art Knives |
Folders | Fighters |
Tomahawks | Miniatures
|